Sandmaster Centrifugal Pumps are crucial equipment in drilling operations. During the oilfield exploitation process, crude oil containing a large amount of sand and gravel needs to be efficiently extracted and transported, making these pumps indispensable. This article will explore the role of Sandmaster Centrifugal Pumps in drilling operations and the key points of their maintenance.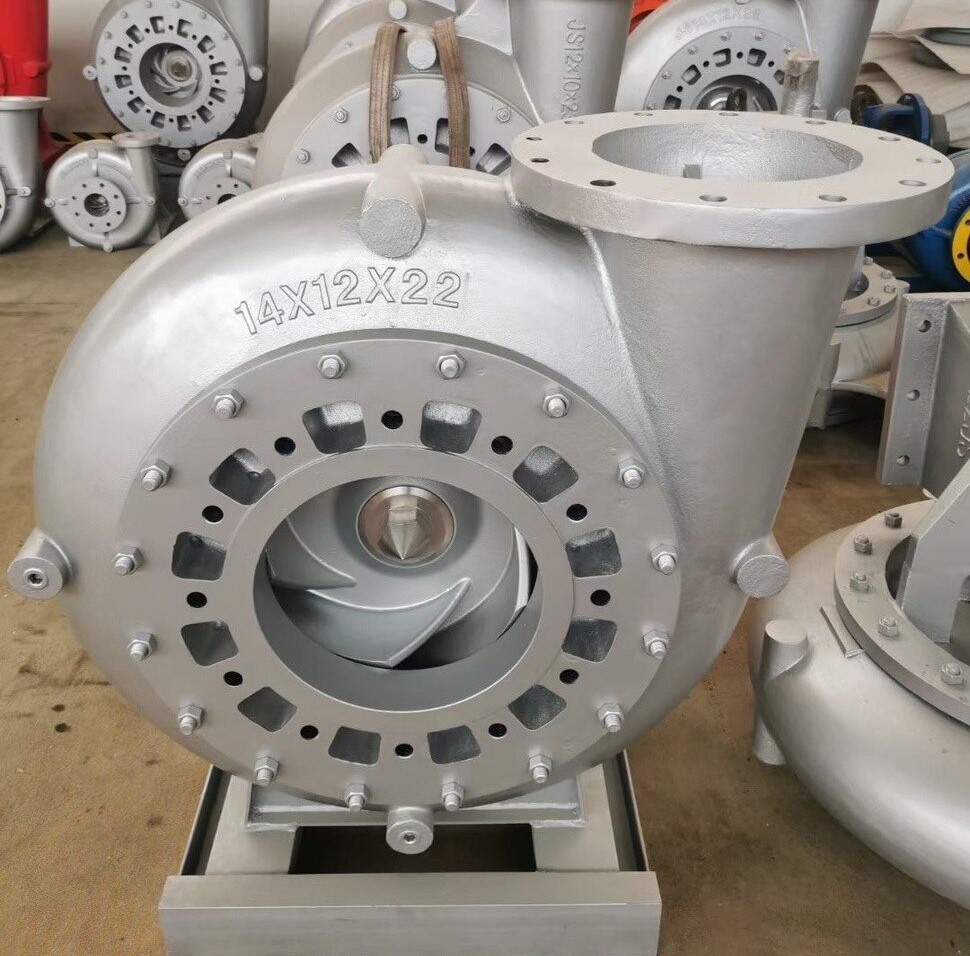
I. Principles and Composition of Sandmaster Centrifugal Pumps
Working Principle
Centrifugal pumps operate by using the centrifugal force generated by the rotation of the impeller to move the liquid. Sandmaster Centrifugal Pumps also work based on the principle of centrifugal force. They consist of a rotating impeller, a fixed pump casing, and inlet and outlet pipes. After the pump is started, the electric motor drives the impeller to rotate. Due to the rotation of the impeller, the mud is pushed towards the outlet of the pump body under the action of centrifugal force and then enters the pipeline for transportation to the target location.
Main Components
Centrifugal Sand Pump Impeller: The impeller is the core component of the pump. Considering the requirements of wear-resistance and corrosion-resistance of the material, most impellers are currently made of cast iron, cast steel, etc. The open-type impeller of a Sandmaster Centrifugal Pump is suitable for transporting fluids containing a large number of solid particles and is not easy to be blocked.
Sand Pump Shaft: The pump shaft is used to rotate the pump impeller and must have sufficient torsional strength and stiffness.
Centrifugal Sand Pump Casing: The pump casing plays a role in supporting and fixing.
Bearings: Bearings are components that are sleeved on the pump shaft to support the pump shaft, enabling the pump shaft to rotate smoothly and reducing the frictional resistance during rotation.
Sand Pump Sealing Ring (also known as Leak-reducing Ring): In order to increase the reflux resistance, reduce internal leakage, and extend the service life of the impeller and the pump casing, a sealing ring is installed at the joint of the inner edge of the pump casing and the outer edge of the impeller.
II. Advantages of Sandmaster Centrifugal Pumps
High - efficiency Pumping Capacity: Sandmaster Centrifugal Pumps can separate the liquid carrying solid particles by using centrifugal force and effectively handle these solid particles. They can provide sufficient flow rate and pressure to meet the needs during the drilling process.
Stable Operation in Harsh Environments: Sandmaster Centrifugal Pumps usually adopt high-quality materials and advanced manufacturing processes. They can prevent the wear and blockage of the internal transmission components by particles, reduce the number of downtime for maintenance, improve work efficiency and production capacity, and can operate stably in harsh working environments.
Simple Maintenance: The maintenance of Sandmaster Centrifugal Pumps is relatively simple. Only regular cleaning and lubrication are required to ensure their normal operation.
III. Maintenance and Repair of Sandmaster Centrifugal Pumps: Suggestions and Precautions
Regular Inspection and Replacement of Worn Parts
Since Sandmaster Centrifugal Pumps are often used to handle fluids with a high solid content, components such as the pump cavity, impeller, and others may be subject to wear. Therefore, it is necessary to regularly inspect and replace worn parts.
Cleaning the Inside of the Pump
After long-term use, particles may accumulate inside the Sandmaster Centrifugal Pump. Regularly cleaning the inside of the pump can prevent blockages and reduce the occurrence of pump failures.
Checking the Lubrication System
Regularly check the working status of the lubrication system to ensure that the lubricating oil is sufficient and of good quality.
Operations during Shutdown
Before shutting down, reduce the pump's rotational speed and pressure, close the corresponding valves, and cut off the power source. If possible, try to empty the fluid in the pump cavity to reduce the corrosion and damage of the remaining medium to the pump components.
IV. Handling Special Situations
Handling Sand Blockages
If it is found that the pump's performance deteriorates or abnormal vibrations occur due to sand blockages, stop the machine immediately, disassemble the pump body, and clean the sand inside. At the same time, check whether the filter is damaged and repair or replace it in a timely manner if it is damaged.
Handling Corrosion
For the corrosion of pump body components caused by transporting corrosive fluids, corresponding measures should be taken according to the degree of corrosion. For mild corrosion, an anti-corrosion coating treatment can be carried out; for severely corroded components, they must be replaced in a timely manner.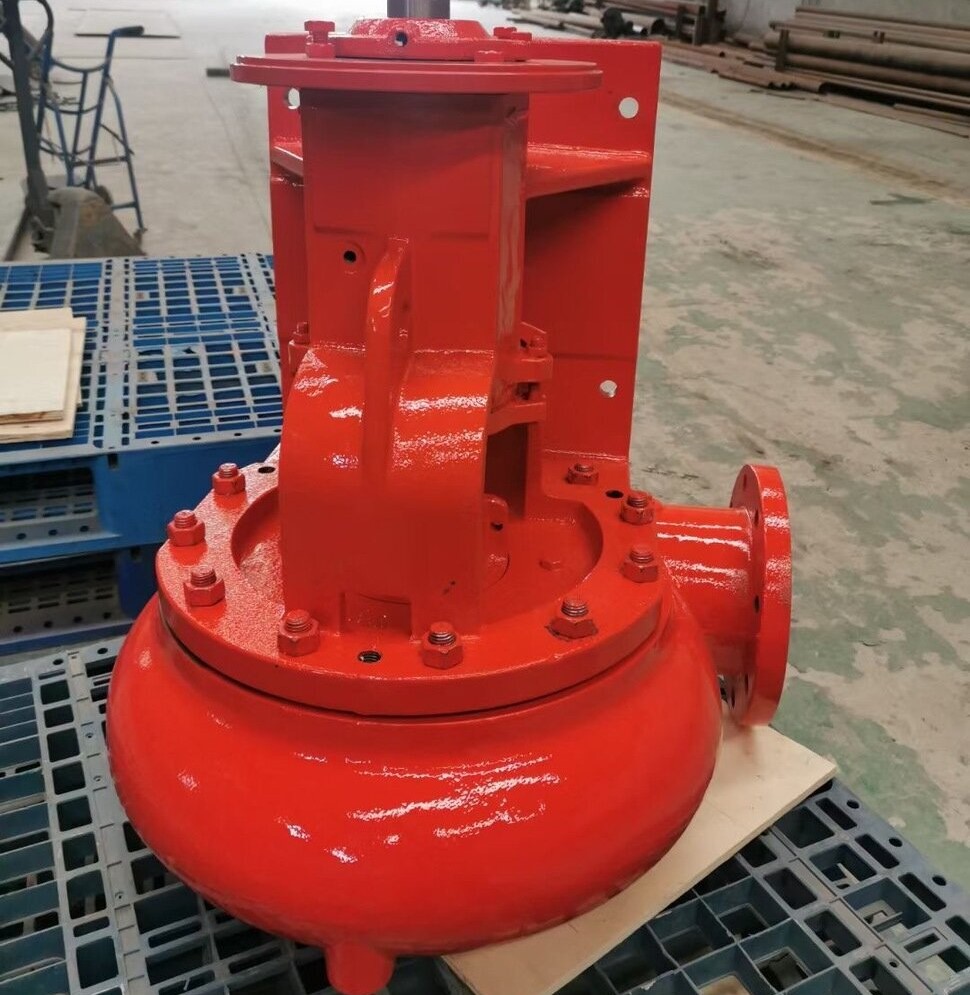
V. Selection Points
Common models of Sandmaster Centrifugal Pumps of the Mission brand are as follows:
3x2x13: It is usually suitable for occasions where the requirements for flow rate and head are relatively low, but a certain sand-containing fluid needs to be handled, such as small-scale industrial wastewater treatment systems, mud transportation in construction projects, and other small-scale operations.
4x3x13: It has a slightly larger flow rate and head than 3x2x13. It can be used in some small-scale slurry transportation lines in industries such as mining and metallurgy, or as a supporting pump for small-scale sand-removal equipment.
5x4x14: It can handle a larger flow of sand-containing fluid. In some medium-scale oil extraction operations, it can be used as a sand-liquid transportation pump near the wellhead, and can also be used for the preliminary lifting and transportation of sand-containing sewage in urban sewage treatment plants.
6x5x11 and 6x5x14: The head of 6x5x11 is relatively low and may be more suitable for the short-distance and large-flow transportation of sand-containing fluids, such as the transportation of sand-water mixtures in river dredging projects; 6x5x14 has a higher head and can be used for occasions where the sand-containing fluid needs to be lifted to a certain height, such as the transportation of tailings in mines to a high-altitude tailings pond.
8x6x11 and 8x6x14: These two models of pumps have large flow rates and high heads. 8x6x11 is more efficient in handling large-flow sand-containing fluids and is often used in large-scale dredgers, port dredging, and other projects; 8x6x14 can be used for large-scale oil-sand transportation in oil extraction, or for the long-distance transportation of high-sand-content slurry in large-scale mines.
10x8x14: It has a large flow rate and a relatively high head and is suitable for the transportation of sand-containing raw materials in large-scale petrochemical projects, or for the main slurry transportation lines in large-scale mines, being able to meet the needs of large-scale and high-head transportation.
12x10x23: It has a very large flow rate and head and is generally used in ultra-large-scale mining, ocean engineering, and other fields. It can cope with extreme working conditions with high sand content, large flow rate, and high head requirements, such as the transportation of sand-ore from deep-sea mining to offshore platforms.