What is a circulation system in drilling?
Apr 11, 2025
The drilling rig circulation system is an extremely important part of oil drilling and other operations. It is mainly responsible for the circulation of drilling fluid to achieve functions such as carrying cuttings, cooling the drill bit, lubricating the drilling tools, and balancing the formation pressure. The following is a detailed introduction:
Ⅰ. Main Components
1.Drilling Pump
- Function: It is the core equipment of the circulation system, used to provide power for the circulation of the drilling fluid. It pumps the drilling fluid from the mud pit into the drill string and then sprays it out through the drill bit nozzles. Common drilling pumps include piston pumps, and the F type drilling mud pump is widely used, which has the characteristics of large displacement and high pressure.
- Type: In common piston pumps, the piston moves back and forth in the cylinder to suck in and discharge the drilling fluid. When the piston moves backward, the volume inside the cylinder increases, the pressure decreases, and the drilling fluid enters the cylinder through the suction valve under the action of atmospheric pressure. When the piston moves forward, the drilling fluid in the cylinder is squeezed, the pressure rises, and the discharge valve is opened to discharge the drilling fluid from the cylinder, thus realizing the suction and discharge process of the drilling fluid. It has the characteristics of large displacement and high pressure and is suitable for various drilling operations.
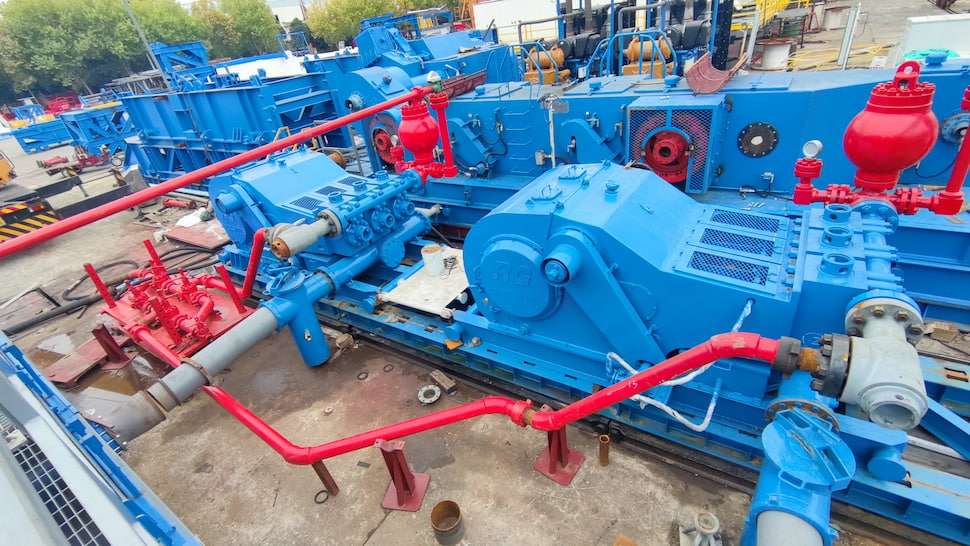
2.Mud Pit and Storage Tank
- Function: The mud pit is used to store the drilling fluid and also plays a role in the preliminary precipitation of cuttings during the circulation of the drilling fluid.The storage tank is used to store a large amount of drilling fluid to meet the circulation requirements during the drilling process. The volume of the mud tank is determined according to the scale and requirements of the drilling operation. Usually, multiple mud tanks are connected to form a complete storage system.
3.Mud Purification Equipment
- It includes drilling fluid shale shakers, desanders, desilters, mud centrifugal pumps, etc. The shale shaker is mainly used to remove larger particles of cuttings in the drilling fluid. The desander and desilter are respectively used to remove smaller particles of sand and mud. The centrifugal mud pump can further separate finer solid particles and weighting materials, purify the drilling fluid, and make it reusable.
4.Drill String and Drill Bit
- The drill string is the passage for the drilling fluid. The drilling fluid flows downward through the inside of the drill string, and after being sprayed out from the nozzles of the drill bit, it carries the cuttings and returns to the surface along the annulus between the wellbore and the drill string. The design of the drill bit nozzles has an important influence on the spraying speed and flow pattern of the drilling fluid, thus affecting the carrying capacity of the cuttings.
The components of the drill string include drill pipes and drill collars.
- Drill Pipe: It is the main component of the drill string, used to connect the swivel and the drill bit to form a passage for the drilling fluid. Drill pipes are usually made of high-strength alloy steel, which has high strength and toughness and can withstand various loads such as tension, compression, and torsion during the drilling process. Special threads are processed at both ends of the drill pipe for connecting adjacent drill pipes and other drilling tools.
- Drill Collar: It is generally located at the lower part of the drill string, close to the drill bit. The main function of the drill collar is to provide sufficient weight on bit (WOB) for the drill bit so that the drill bit can effectively break the rock. The drill collar is usually shorter and thicker than the drill pipe, with a large weight and stiffness, which can maintain a stable posture during the drilling process and prevent excessive bending and swinging of the drill string.
5.Surface Manifolds
- It connects various components such as the drilling pump, drill string, mud purification equipment, and mud pit, forming a passage for the circulation of the drilling fluid. The surface manifolds need to have good sealing performance and pressure resistance to ensure the smooth circulation of the drilling fluid.
- Suction Manifold: It connects the mud tank and the inlet of the drilling pump and is used to smoothly transport the drilling fluid in the mud tank to the drilling pump. The suction manifold usually includes suction pipelines, suction valves, filters, and other components. The filter can prevent large-particle impurities from entering the drilling pump and avoid damage to the pump.
- Discharge Manifold: It transports the high-pressure drilling fluid discharged from the drilling pump to the standpipe and subsequent equipment. Various valves such as safety valves, throttle valves, and mud gate valves are installed on the discharge manifold to control the flow rate, pressure, and flow direction of the drilling fluid. The safety valve can automatically open to release the pressure when the system pressure is too high to protect the equipment safety. The throttle valve is used to precisely adjust the flow rate of the drilling fluid to meet the needs of different drilling conditions.
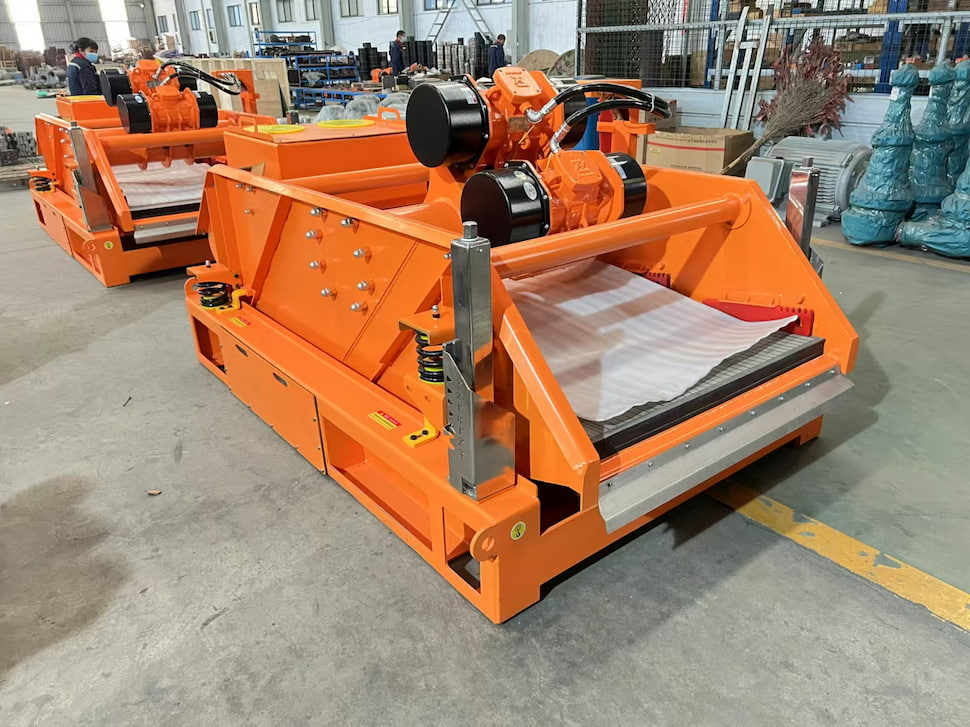
6.Standpipe and Hose
- Standpipe: It is a vertical pipe installed beside the derrick, which transports the high-pressure drilling fluid in the surface manifolds to the upper part of the wellhead. The standpipe is usually made of high-strength steel pipes and can withstand the pressure of high-pressure drilling fluid. For the convenience of installation and maintenance, the standpipe is generally composed of multiple sections, and the sections are connected by flanges or threads.
- Hose: It is a flexible high-pressure hose connecting the standpipe and the swivel. The hose has good flexibility and pressure resistance and can swing flexibly with the up-and-down movement and rotation of the drilling tools to ensure that the drilling fluid can be smoothly transported from the standpipe to the drill string. The inside of the hose is usually made of wear-resistant and corrosion-resistant materials to extend its service life.
7.Swivel
- Rotation Function: It allows the drill string to move up and down while rotating, enabling the drilling fluid to enter the inside of the drill string through the swivel. The rotating part of the drilling rotary swivel uses high-precision bearings and sealing devices, which can maintain good sealing performance and stability in a high-speed rotation and high-pressure environment.
- Loading Function: It bears the weight of the drill string and various axial and radial forces generated during the drilling process. The outer shell and internal structure of the swivel have sufficient strength and stiffness to ensure safe and reliable operation throughout the drilling process.
Ⅱ. Overall Working Principle
The drilling pump sucks the treated drilling fluid from the mud tank and enters the pump body through the suction manifold. Under the action of the pump, the drilling fluid is pressurized to the required pressure and then transported to the standpipe through the discharge manifold. The standpipe transports the high-pressure drilling fluid vertically upward to the hose at the top of the derrick. The hose introduces the drilling fluid into the swivel, and the swivel distributes the drilling fluid into the inside of the drill string.
The drilling fluid flows downward along the axis inside the drill string. After reaching the drill bit, it is sprayed out at a high speed from the nozzles of the drill bit. The design of the nozzles enables the drilling fluid to impact the rock at the bottom of the well at a high speed to assist the drill bit in breaking the rock. At the same time, after being sprayed out from the drill bit, the drilling fluid carries the cuttings at the bottom of the well and enters the annulus between the drill string and the wellbore together.
In the annulus, the drilling fluid carries the cuttings and flows upward to return to the surface. The drilling fluid returning to the surface enters the mud tank through the surface manifolds. In the mud tank, the drilling fluid is first agitated by the agitator to keep the solid particles in suspension. Then, it passes through treatment equipment such as the desander, desilter, and centrifuge in turn to remove the cuttings, sand particles, and other harmful components. The treated drilling fluid is sucked in by the drilling pump again to start a new cycle.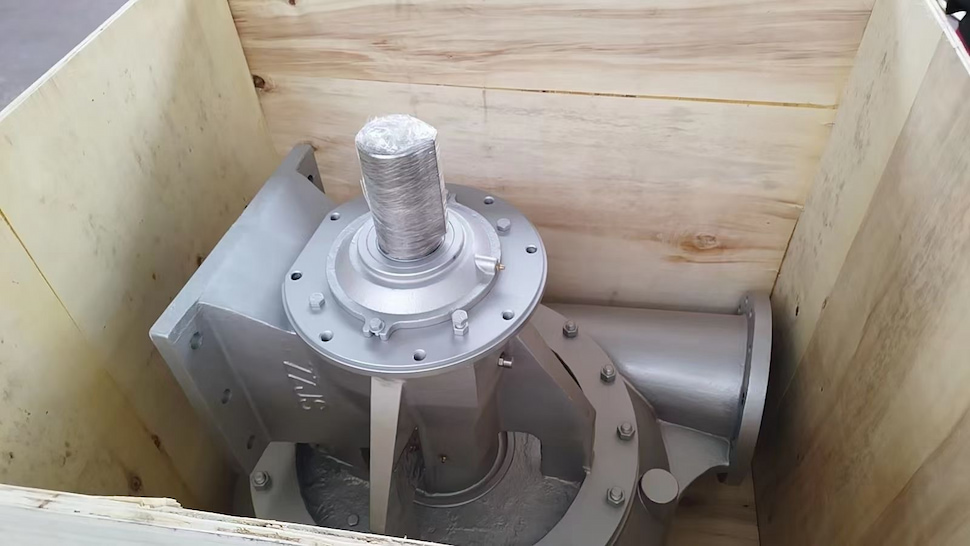
Ⅲ. Function and Importance
- Carrying Cuttings: It timely carries the cuttings broken by the drill bit from the bottom of the well to the surface, preventing the cuttings from accumulating at the bottom of the well and affecting the drilling efficiency and the service life of the drill bit.
- Cooling and Lubricating: During the circulation process, the drilling fluid can take away the heat generated by the drill bit and the drill string during the drilling process, playing a cooling role. At the same time, it can also form a lubricating film between the drill string and the wellbore, reducing the frictional resistance and reducing the wear of the drilling tools.
- Balancing Formation Pressure: The drilling fluid with appropriate performance can balance the formation pressure, prevent formation fluids (such as oil, gas, and water) from flowing into the wellbore, avoid accidents such as blowouts, and ensure the safety of the drilling operation.
- Protecting the Wellbore Wall: The mud cake formed by the drilling fluid on the wellbore wall can play a role in stabilizing the wellbore wall, preventing the wellbore wall from collapsing, and maintaining the integrity of the wellbore.
Ⅳ. Maintenance Points
- Maintenance of the Drilling Pump: Regularly check the wear conditions of vulnerable parts such as the piston, cylinder liner, and valve seat of the pump, and replace the severely worn parts in a timely manner. Keep the lubrication system and cooling system of the pump working normally. Regularly check the oil level and quality of the lubricating oil to ensure that the cooling water is sufficient. In addition, it is also necessary to regularly clean the pump to prevent impurities such as mud from accumulating on the surface and inside of the pump body.
- Maintenance of the Manifolds: Check whether there are leakage phenomena at the connection parts of the manifolds, and tighten the loose bolts or replace the seals in a timely manner. Regularly clean the dirt and debris inside the manifolds to prevent them from blocking the pipelines. Maintain the valves on the manifolds to ensure that the valves can be opened and closed flexibly and have good sealing performance. Regularly lubricate and maintain the valves to prevent the valves from rusting and jamming.
- Maintenance of the Standpipe and Hose: Check whether the fixing of the standpipe is firm and whether there are deformation or corrosion phenomena. Regularly check the welds of the standpipe to prevent the occurrence of defects such as cracks. Avoid excessive bending and stretching of the hose. Regularly check whether there are damages such as cracks and bulges on the surface of the hose. If there is any damage, it should be replaced in a timely manner. At the same time, keep the hose clean and avoid impurities such as mud adhering to the surface, which will affect its performance.
- Maintenance of the Swivel: Regularly check the rotating part and the sealing part of the swivel to ensure that it rotates flexibly and has good sealing performance. Lubricate and maintain the bearings of the swivel and replace the lubricating grease regularly. Check whether there are cracks or deformations in components such as the bail and gooseneck of the swivel. If there are any problems, they should be repaired or replaced in a timely manner.
- Maintenance of the Drill String: During the tripping operation, pay attention to the operation specifications to avoid excessive impact and bending of the drill string. Regularly check whether the threads of the drill pipe and drill collar are worn, deformed, or damaged, and clean, grease, and repair the threads in a timely manner. Conduct non-destructive testing on the drill string to check whether there are defects such as cracks inside to ensure the safety and reliability of the drill string.
- Maintenance of the Mud Tank: Regularly clean the sand and debris in the mud tank to keep the tank clean. Check whether the blades of the agitator are worn, and replace the damaged blades in a timely manner to ensure the normal operation of the agitator. Carry out anti-corrosion treatment on the tank body of the mud tank to prevent the tank body from being corroded by the drilling fluid. At the same time, regularly check whether the instruments such as the level gauge and thermometer of the mud tank are working normally to ensure that the parameters of the drilling fluid can be accurately measured and monitored.